Introduction
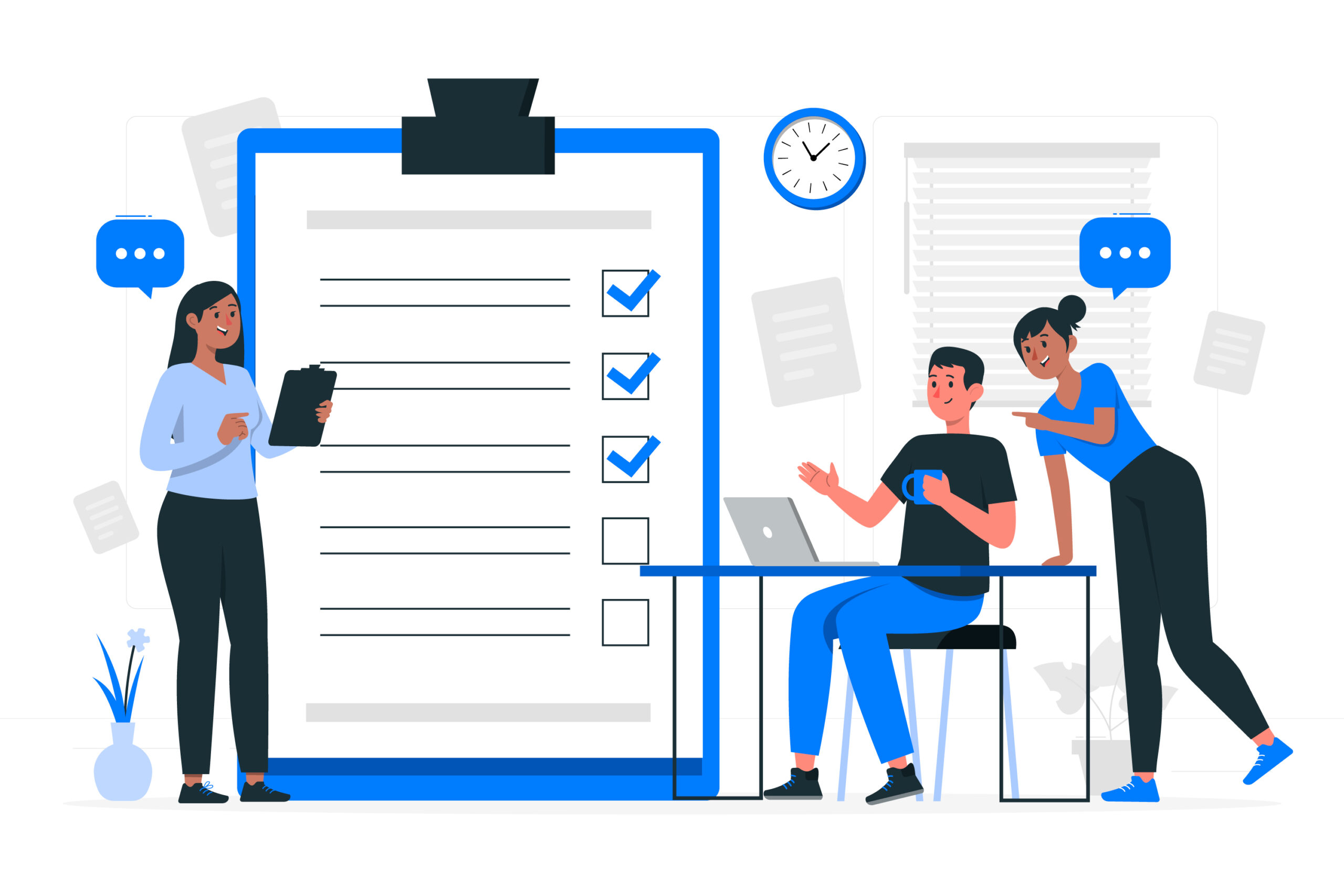
Unplanned downtime and emergency repairs are critical challenges for industries relying on complex machinery and equipment. These unexpected interruptions can cause significant financial losses, operational disruptions, and safety hazards. In this blog, we will explore the pain points associated with unplanned downtime and emergency repairs and introduce predictive maintenance technologies as a comprehensive solution to these issues.
The Problem: Unplanned Downtime and Emergency Repairs
Unplanned downtime occurs when machinery or equipment fails unexpectedly, halting operations and causing a cascade of negative effects. Here are the key impacts of unplanned downtime and emergency repairs:
1. Financial Impact: The cost of unplanned downtime is substantial. It includes lost production, idle labor, and the expense of emergency repairs. For example, in the manufacturing sector, even a few hours of downtime can result in losses amounting to hundreds of thousands of dollars.
2. Operational Disruption: When equipment breaks down unexpectedly, it disrupts the entire production schedule. This can lead to delays in delivering products to customers, causing dissatisfaction and potential loss of business.
3. Increased Repair Costs: Emergency repairs are often more expensive than planned maintenance. This is due to the need for expedited parts, overtime labor, and sometimes even temporary solutions that are not cost-effective in the long term.
4. Safety Risks: Equipment failures can pose serious safety risks to employees. Malfunctions can lead to accidents and injuries, creating additional liabilities and concerns for workplace safety.
5. Reputation Damage: Frequent and prolonged downtimes can damage a company’s reputation. Consistent reliability is crucial for maintaining customer trust and loyalty. Unplanned downtimes signal unreliability and can erode this trust.
The Solution: Predictive Maintenance Technologies
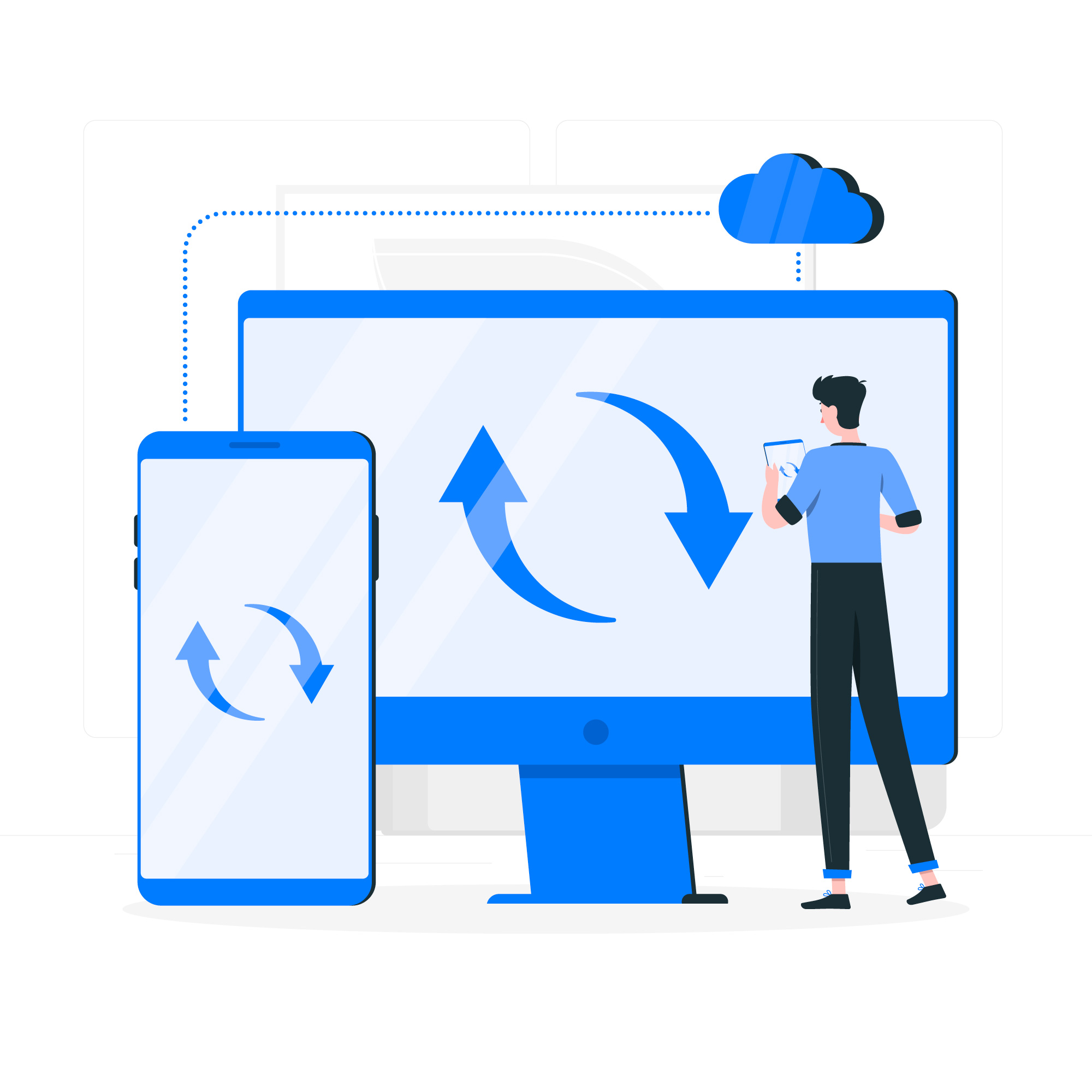
Predictive maintenance (PdM) is a proactive approach that uses data and analytics to predict and prevent equipment failures before they happen. This method leverages advanced technologies to monitor equipment conditions in real-time and analyze data to forecast potential issues. Here’s how predictive maintenance addresses the pain points of unplanned downtime and emergency repairs:
1. Real-Time Monitoring: Sensors and Internet of Things (IoT) devices are installed on machinery to continuously monitor parameters such as temperature, vibration, and pressure. This real-time data collection provides an ongoing health check of the equipment.
2. Data Analytics and Machine Learning: The collected data is analyzed using advanced analytics and machine learning algorithms to detect patterns and anomalies. These technologies can predict when a component is likely to fail, allowing for proactive maintenance.
3. Proactive Maintenance Scheduling: Predictive maintenance enables maintenance teams to schedule repairs and maintenance activities at optimal times, avoiding the disruption of unplanned downtime. This ensures maintenance is performed just in time, based on actual equipment needs rather than fixed schedules.
4. Cost Reduction: By preventing unexpected breakdowns, predictive maintenance reduces the need for costly emergency repairs. It also helps in extending the lifespan of equipment, further saving costs in the long run.
5. Improved Safety and Reliability: Predictive maintenance minimizes the risk of sudden equipment failures, enhancing workplace safety. It ensures that machinery operates reliably, which is crucial for maintaining consistent production quality.
Implementing Predictive Maintenance Technologies
Implementing predictive maintenance requires a strategic approach to ensure its effectiveness and integration into existing operations. Here’s a step-by-step guide to implementing predictive maintenance technologies:
1. Assessment and Planning: Begin by assessing your current equipment and identifying critical assets that would benefit the most from predictive maintenance. Develop a detailed implementation plan that includes objectives, budget, timeline, and required resources.
2. Selecting the Right Technologies: Choose the appropriate predictive maintenance tools and technologies that align with your needs. This includes selecting suitable sensors, IoT platforms, data analytics software, and machine learning solutions.
3. Data Integration: Integrate the predictive maintenance system with your existing enterprise systems such as Enterprise Resource Planning (ERP), Computerized Maintenance Management Systems (CMMS), and Supervisory Control and Data Acquisition (SCADA) systems. Ensure seamless data flow and interoperability between these platforms.
4. Pilot Testing: Conduct a pilot test on a small scale to validate the effectiveness of the predictive maintenance solution. Monitor the performance and gather feedback to make necessary adjustments before full-scale deployment.
5. Full-Scale Deployment: After successful pilot testing, roll out the predictive maintenance solution across all relevant assets. Train your maintenance team and other relevant staff on how to use the new system effectively.
6. Continuous Improvement: Continuously monitor the performance of the predictive maintenance system. Use the insights gained to make improvements and stay updated with advancements in technology to enhance the system further.
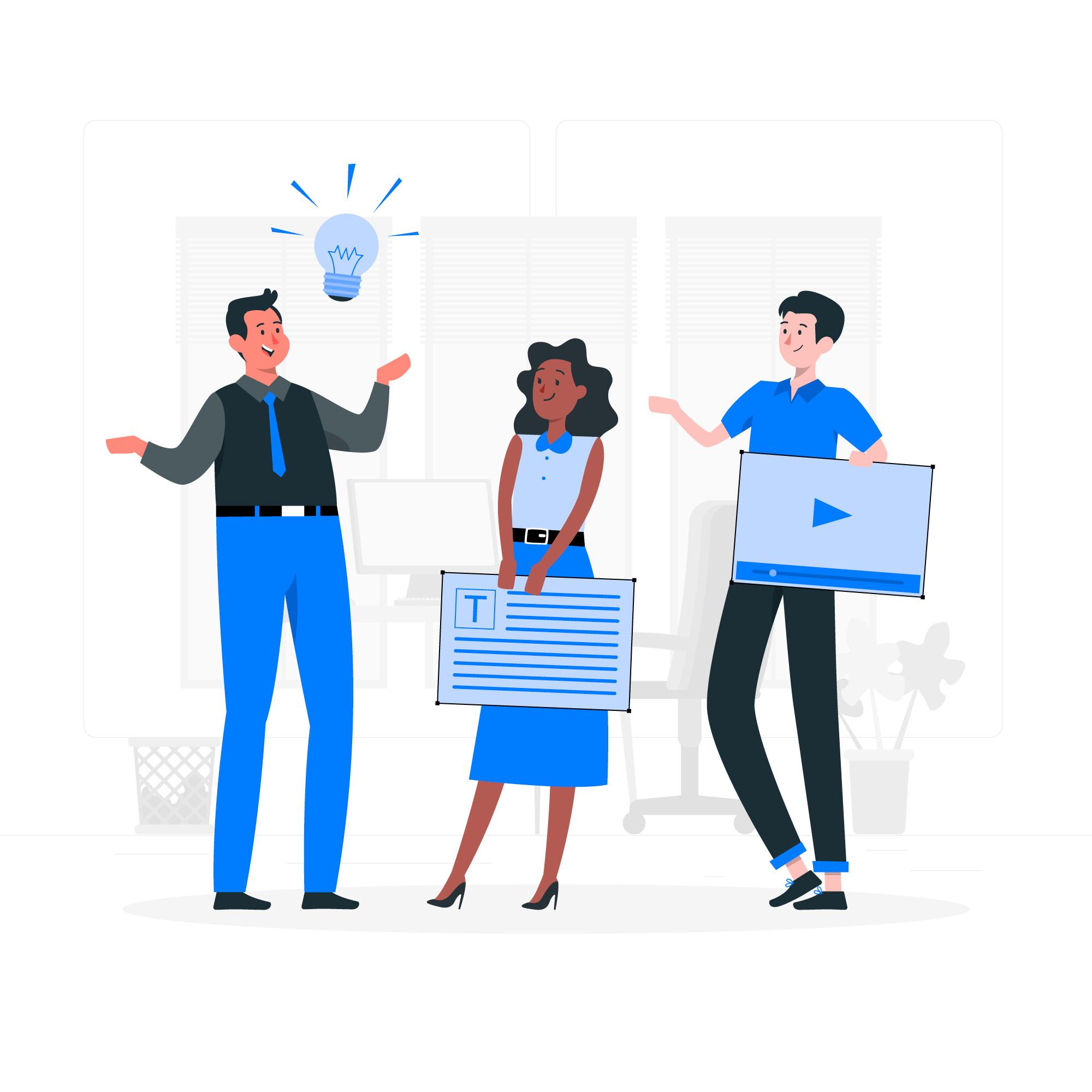
Conclusion
Unplanned downtime and emergency repairs pose significant challenges that can severely impact a company’s financial health, operational efficiency, and reputation. Predictive maintenance technologies offer a proactive and data-driven solution to these issues. By leveraging real-time monitoring, advanced analytics, and machine learning, businesses can anticipate equipment failures, optimize maintenance schedules, and ensure smooth and efficient operations.
Investing in predictive maintenance is not just about reducing costs; it’s about transforming maintenance practices to achieve greater reliability, safety, and competitive advantage in today’s dynamic business environment.
Call to Action
Are you ready to minimize unplanned downtime and improve the reliability of your operations? Contact us today to learn more about our predictive maintenance solutions and how they can benefit your business. Let’s work together to keep your machinery running smoothly and your operations efficient.